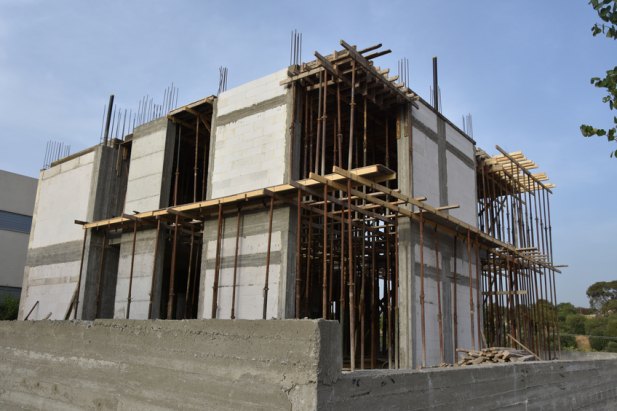
Prefab Construction: When it Makes Sense, and When it Doesn’t
The popularity of pre-fabrication construction is growing, in large part due to a shortage of construction laborers. Experts project that construction will grow six percent this year, yet the labor shortage could potentially delay those projects. The reason behind the shortfall is multifaceted: many construction workers left the industry during the real estate crash a handful of years ago. At the same time, veteran construction laborers are retiring from the industry while fewer young people are entering the trades. The resulting fallout, according to the Associated General Contractors, is that 86 percent of commercial builders are finding it challenging to fill their positions.
Prefabricated construction, also known as modular construction, is a possible way to span the gap. With prefab construction, several of a project’s components are built in a factory and assembled when needed, reducing the need for laborers at the construction site. These days prefab covers a wide range of industrial, commercial and residential construction. But is prefab the right choice for you? Here’s a look at some primary considerations.
When Prefab May Make Sense
When you want to save money. Prefab construction costs can be significantly lower in cost than conventional construction. Experts say efficiencies realized on the assembly line translate into cost savings as compared to site-built construction.
When you want to save time. Modular buildings can be assembled much faster than site-built construction. While conventional projects have linear schedules, modular construction allows contractors to work on several aspects of the project concurrently. In addition, factory construction does not experience weather-related delays, unlike construction site work. As a result modular construction can reduce the construction phase duration as compared to a site-built project.
When you want to save the environment. The Modular Building Institute reports that prefab and modular construction reduces material waste, cuts the pollution of air and water, and reduces energy use.
When Prefab May Not Work for You
If the scope of the project increases associated costs. Depending on the size of the construction, shipping of the modules can drive up costs, as well as craning on-location. In addition, oversized loads can also carry higher costs due to necessary safety measures. Shipping distance also plays a role.
If your project design has not been finalized. Prior to commencing prefab construction, the design of your project must be complete. Also, changes in design after commencing the assembly of building components is difficult and can be costly in time and money. If you are unsure of your project design details, then prefab construction may not preferable.
If you subscribe to the lingering stigma. Owners may be concerned about the quality of construction, because historically this has been an issue. In fact, today’s modular buildings are constructed using the same materials as site-built construction, and they meet, and often exceed, design specs.
When considering managing your project schedule, prefab construction can be a viable alternative to site-built construction, depending on your project. A reputable builder can help guide you in the right direction and through the process.